1. Understanding Modern Scaffolding Systems
Modern scaffolding systems combine innovative design with robust safety features. Key advances include modular components, integrated fall protection, and smart monitoring capabilities. Understanding these systems is crucial for maintaining workplace safety and operational efficiency.
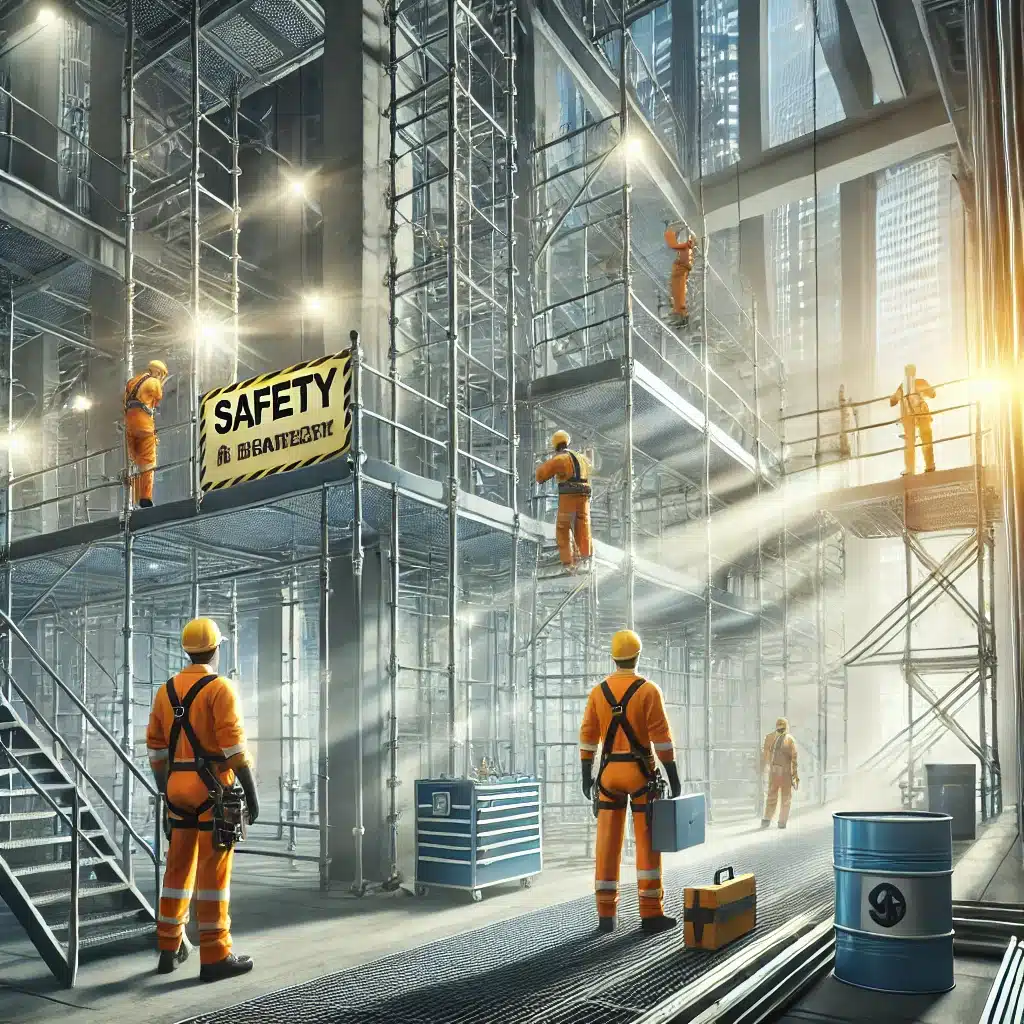
1.1 Components of Quality Scaffolding
Quality scaffolding begins with essential components engineered to precise specifications. Standards, ledgers, and transoms form the primary framework, while base plates distribute loads evenly to the ground. These components must meet strict material grade requirements and undergo regular testing for structural integrity.
Modern scaffolding incorporates advanced connection systems that enhance stability while reducing assembly time. Quick-lock mechanisms, reinforced joints, and precision-engineered couplers ensure rigid connections between components, while allowing for rapid deployment and dismantling when needed.
When sourcing quality scaffolding components, established suppliers like National Site Supplies offer comprehensive systems that meet these rigorous specifications.
1.2 Material Standards and Specifications
Material selection follows stringent industry standards, with steel grades carefully chosen for optimal strength-to-weight ratios. Common specifications include:
Component | Material Grade | Minimum Yield Strength |
---|---|---|
Standards | S355 Steel | 355 MPa |
Platforms | Aluminum 6082-T6 | 260 MPa |
Connectors | High-tensile Steel | 480 MPa |
Base Plates | Ductile Iron | 400 MPa |
Quality control processes ensure materials meet these specifications through batch testing and certification procedures. Regular material testing includes non-destructive evaluation methods and stress analysis to verify ongoing compliance.
1.3 Innovation in Scaffolding Design
Recent innovations focus on enhancing safety through design improvements. Integrated guardrail systems, self-locking platforms, and load-sensing technologies represent significant advances in scaffolding safety. These innovations reduce human error risks while improving efficiency.
Smart scaffolding systems now incorporate IoT sensors for real-time monitoring of structural integrity and load distribution. These systems can alert supervisors to potential safety issues before they become critical, enabling proactive maintenance and risk management.
1.4 Compatibility and Integration
System compatibility ensures seamless integration between components from different manufacturers or production batches. Standard interfaces and universal connection points allow for:
- Interchangeable components
- Modular expansions
- Simplified maintenance
- Reduced equipment inventory
Standardization efforts have led to improved compatibility across manufacturers, though careful attention must be paid to certification and load ratings when mixing components.
2. Essential Safety Features and Equipment
Modern scaffolding incorporates multiple layers of safety features designed to protect workers and maintain structural integrity. From basic guardrails to advanced fall protection systems, each component plays a crucial role in workplace safety.
2.1 Fall Prevention Systems
Primary fall prevention features include guardrails, mid-rails, and toe boards installed at all working levels. These systems must meet minimum height requirements:
- Guardrails: 42 inches (±3 inches)
- Mid-rails: 21 inches
- Toe boards: 4 inches minimum height
Secondary fall protection includes personal anchor points and safety harness systems rated for fall arrest. These systems require regular inspection and certification to maintain their effectiveness.
2.2 Load-Bearing Components
Load-bearing elements must meet specific capacity requirements based on intended use:
Component | Minimum Load Capacity | Safety Factor |
---|---|---|
Platforms | 75 lbs/sq ft | 4:1 |
Standards | 12,000 lbs | 3:1 |
Connectors | 5,000 lbs | 5:1 |
Regular load testing verifies these capacities remain within specifications. Documentation of testing results must be maintained and readily available for inspection.
2.3 Access and Egress Solutions
Safe access requires properly designed ladders, stairs, or ramps meeting specific angle and dimension requirements. Access points must be placed at maximum intervals of 50 feet horizontally and must include rest platforms at vertical intervals not exceeding 35 feet.
Egress routes require clear marking and unobstructed paths to ensure quick evacuation in emergencies. Emergency lighting and signage must be maintained at all access points and along evacuation routes.
2.4 Weather Protection Features
Environmental protection systems include wind screens, debris netting, and weather shelters. These features must be:
- Rated for local wind conditions
- Fire-retardant where required
- Properly secured to prevent displacement
- Regularly inspected for damage
Installation methods must account for additional wind loads and ensure proper water drainage to prevent pooling.
3. Implementing a Comprehensive Maintenance Program
A successful maintenance program combines regular inspections, preventive maintenance, and detailed documentation. This systematic approach ensures equipment reliability and compliance while extending scaffold lifespan.
3.1 Daily Inspection Protocols
Daily inspections follow a structured checklist covering structural integrity, safety features, and access components. Key inspection points include joint connections, platform stability, guardrail security, and base plate conditions.
Documentation of daily inspections must include inspector identification, date/time, findings, and corrective actions. Digital inspection tools now enable real-time reporting and immediate notification of safety concerns.
3.2 Preventive Maintenance Schedules
Preventive maintenance follows manufacturer-specified intervals and procedures:
Component | Inspection Frequency | Maintenance Type |
---|---|---|
Connections | Weekly | Tightening/Cleaning |
Platforms | Monthly | Surface Treatment |
Base Plates | Quarterly | Level Adjustment |
Safety Features | Bi-weekly | Function Testing |
Scheduled maintenance activities must account for environmental conditions and usage patterns that may accelerate wear.
3.3 Documentation and Record-Keeping
Maintenance records must include:
- Equipment identification
- Service dates
- Work performed
- Parts replaced
- Inspector certification
- Follow-up requirements
Digital record-keeping systems enable better tracking and analysis of maintenance patterns while ensuring regulatory compliance.
3.4 Equipment Lifecycle Management
Lifecycle management involves tracking equipment age, usage history, and repair frequency. Equipment reaching end-of-life requires:
- Performance evaluation
- Cost-benefit analysis
- Replacement planning
- Proper disposal procedures
4. Risk Assessment and Safety Planning
Effective risk assessment combines site-specific analysis with comprehensive safety protocols. This proactive approach identifies potential hazards and establishes control measures before work begins.
4.1 Site-Specific Safety Analysis
Site analysis evaluates:
- Ground conditions
- Overhead hazards
- Adjacent structures
- Traffic patterns
- Environmental factors
Risk matrices quantify hazard likelihood and potential impact, guiding control measure selection.
4.2 Environmental Considerations
Environmental risk factors include:
Factor | Impact | Control Measure |
---|---|---|
Wind | Stability | Wind screens |
Rain | Slip hazards | Non-slip surfaces |
Temperature | Material stress | Expansion joints |
Lightning | Electrical risk | Grounding systems |
Monitoring systems track environmental conditions and trigger protective measures when thresholds are exceeded.
4.3 Emergency Response Procedures
Emergency protocols must address:
- Fall incidents
- Structural failure
- Weather emergencies
- Medical emergencies
- Evacuation procedures
Regular drills ensure worker familiarity with emergency procedures and equipment.
4.4 Worker Training Requirements
Required training includes:
- Basic scaffold safety
- Assembly/disassembly procedures
- Equipment inspection
- Emergency response
- Site-specific hazards
Certification tracking ensures all workers maintain current qualifications.
5. Regulatory Compliance and Standards
Compliance frameworks combine government regulations with industry standards to establish minimum safety requirements. Understanding and implementing these requirements is essential for legal operation.
5.1 Current Safety Regulations
OSHA standards establish minimum requirements for scaffold construction, inspection, and use. Key regulations cover load capacities, guardrail specifications, and fall protection requirements. Regular updates to these standards reflect emerging safety concerns and technological advances.
Compliance requires understanding both federal and state-specific requirements. Organizations must maintain current knowledge of regulatory changes and implement updates to safety protocols accordingly.
5.2 Industry Best Practices
Industry standards often exceed regulatory minimums:
Area | Regulatory Minimum | Best Practice |
---|---|---|
Inspections | Daily | Pre/Post shift |
Training | Annual | Quarterly |
Load Testing | As needed | Monthly |
Documentation | Basic records | Digital tracking |
Leading organizations implement these enhanced standards to improve safety outcomes and operational efficiency.
5.3 Certification Requirements
Worker certification requirements include:
- Basic scaffold safety training
- Assembly/disassembly qualification
- Inspection certification
- Specialized equipment training
- Regular recertification
Certification tracking systems ensure compliance and trigger renewal notifications.
5.4 Legal Responsibilities
Legal obligations extend to:
- Equipment owners
- Site supervisors
- Safety managers
- Workers
- Contractors
Documentation systems must track responsibility assignments and maintain liability records.
6. Quality Control in Scaffolding Equipment
Quality control encompasses material testing, manufacturing oversight, and supplier evaluation. These processes ensure equipment meets safety standards throughout its lifecycle.
6.1 Material Testing Standards
Testing protocols include:
- Tensile strength analysis
- Impact resistance testing
- Fatigue testing
- Corrosion resistance
- Non-destructive evaluation
Results must meet ISO and ASTM standards for construction equipment.
6.2 Manufacturing Quality Assurance
Quality assurance steps include:
Stage | Control Measure | Documentation |
---|---|---|
Design | FEA Analysis | Design specs |
Production | In-line testing | QC reports |
Assembly | Load testing | Test certificates |
Shipping | Inspection | Delivery records |
Manufacturing facilities must maintain ISO 9001 certification.
6.3 Equipment Certification Process
Certification requires:
- Material verification
- Design validation
- Production testing
- Third-party inspection
- Documentation review
Regular recertification maintains equipment safety status.
6.4 Supplier Evaluation Criteria
Key supplier metrics:
- Quality consistency
- Delivery reliability
- Technical support
- Compliance history
- Financial stability
Annual supplier audits ensure continued performance.
7. Advanced Safety Technologies
Modern scaffold systems integrate digital monitoring and automated safety features. These technologies enhance traditional safety measures while providing real-time data for decision-making.
7.1 Digital Monitoring Systems
IoT sensors monitor:
- Structural loads
- Environmental conditions
- Access control
- Equipment status
- Safety compliance
Data integration enables predictive maintenance and risk assessment.
7.2 Smart Safety Features
Advanced features include:
- Auto-locking mechanisms
- Load detection systems
- Environmental monitoring
- Emergency alerts
- Access control systems
Integration with building management systems enhances overall site safety.
7.3 Automated Inspection Tools
Digital inspection tools provide:
- Real-time reporting
- Photo documentation
- Defect tracking
- Maintenance scheduling
- Compliance verification
Cloud-based systems enable remote monitoring and analysis.
7.4 Future Safety Innovations
Emerging technologies include:
- AI-powered monitoring
- Augmented reality training
- Drone inspections
- Smart PPE integration
- Predictive analytics
Research focuses on enhancing automation and reducing human error.
8. Cost-Benefit Analysis of Safety Investment
Safety investments generate returns through reduced incidents, improved efficiency, and lower insurance costs. Comprehensive analysis helps justify safety-related expenditures.
8.1 Safety ROI Calculations
ROI factors include:
- Incident reduction
- Insurance savings
- Productivity gains
- Equipment longevity
- Compliance costs
Five-year ROI typically exceeds 300% for comprehensive safety programs.
8.2 Insurance Considerations
Insurance benefits include:
- Premium reductions
- Coverage improvements
- Risk rating benefits
- Claims reduction
- Liability protection
Documentation of safety measures supports insurance negotiations.
8.3 Productivity Benefits
Safety improvements increase:
- Worker efficiency
- Equipment uptime
- Project completion rates
- Client satisfaction
- Contract retention
Measurement systems track productivity gains from safety investments.
8.4 Long-term Cost Savings
Strategic benefits include:
- Reduced maintenance costs
- Lower replacement rates
- Decreased training needs
- Improved reputation
- Enhanced competitiveness
Annual cost savings typically range from 15-25% of safety investment value.